BREEAM is only one side of the (green) coin
ESG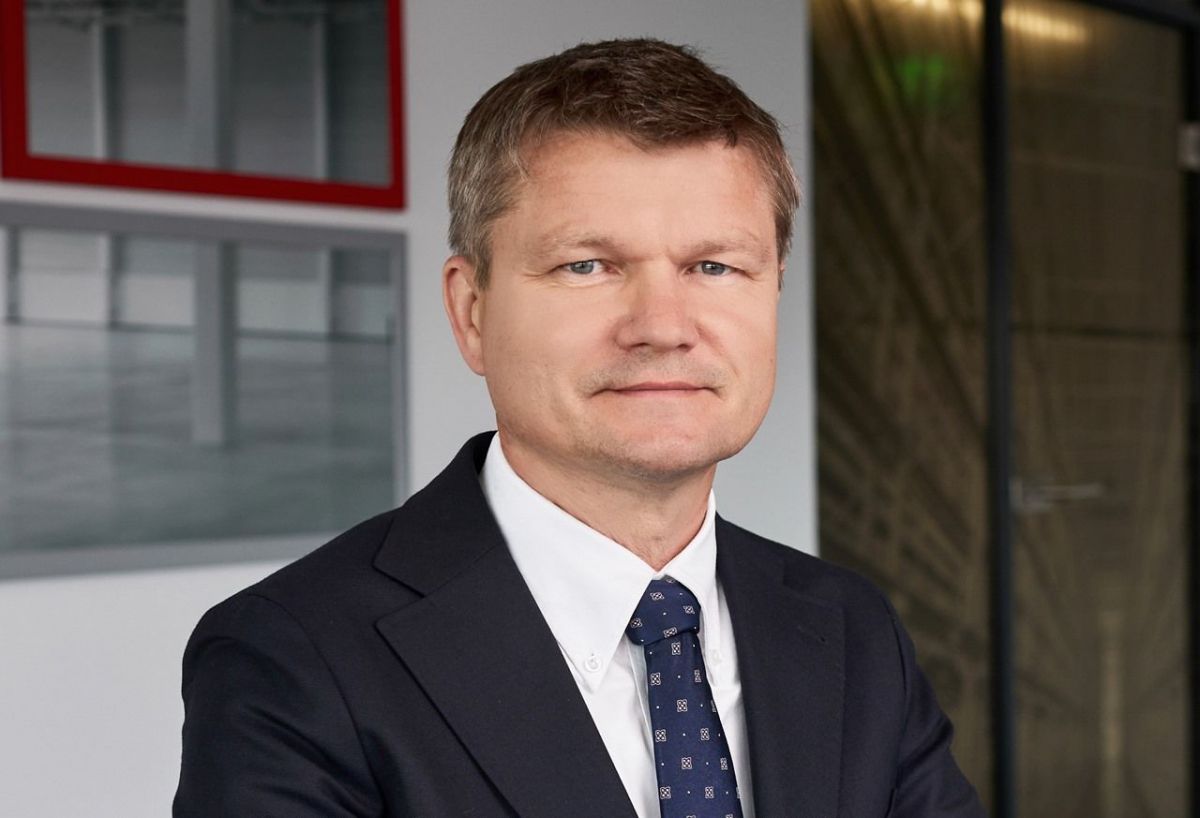
- Access to EurobuildCEE magazine edition online & flipbook version
- Access to EurobuildCEE magazine edition online & flipbook version
- Exclusive news, comments, articles and interviews with the most important market representatives and experts
- Archive containing data and information from the commercial real estate and construction market in Poland and the CEE region, collected over 27 years;
- Eurojobs
- Eurobuild FM